Instituti Francez i Energjisë Diellore Ines ka zhvilluar module të reja PV me termoplastikë dhe fibra natyrale të buruara në Evropë, të tilla si liri dhe bazalti. Shkencëtarët synojnë të zvogëlojnë gjurmën mjedisore dhe peshën e paneleve diellore, ndërsa përmirësojnë riciklimin.
Një panel qelqi i ricikluar në pjesën e përparme dhe një përbërës prej liri në anën e pasme
Imazhi: GD
Nga revista PV Francë
Studiuesit në Institutin Kombëtar të Energjisë Diellore të Francës (INES)-një ndarje e energjisë alternative franceze dhe Komisioni i Energjisë Atomike (CEA)-po zhvillojnë module diellore që shfaqin materiale të reja me bazë bio në anët e përparme dhe të pasme.
"Ndërsa gjurmët e karbonit dhe analiza e ciklit jetësor tani janë bërë kritere thelbësore në zgjedhjen e paneleve fotovoltaike, burimi i materialeve do të bëhet një element thelbësor në Evropë në vitet e ardhshme," tha Anis Fouini, drejtori i CEA-iines , në një intervistë për revistën PV France.
Aude Derrier, koordinatori i projektit hulumtues, tha që kolegët e saj kanë shikuar materialet e ndryshme që ekzistojnë tashmë, për të gjetur një që mund të lejojë prodhuesit e modulit të prodhojnë panele që përmirësojnë performancën, qëndrueshmërinë dhe koston, ndërsa ulin ndikimin në mjedis. Demonstruesi i parë përbëhet nga qelizat diellore heterojunction (HTJ) të integruara në një material gjithëpërfshirës.
"Ana e përparme është bërë nga një polimer i mbushur me fije qelqi, i cili siguron transparencë," tha Derrier. "Ana e pasme është bërë nga e përbëra bazuar në termoplastikë në të cilën është integruar një gërshetim i dy fibrave, liri dhe bazalt, i cili do të sigurojë forcë mekanike, por edhe rezistencë më të mirë ndaj lagështisë."
Liri është me burim nga Franca veriore, ku i gjithë ekosistemi industrial është tashmë i pranishëm. Basalti është buruar diku tjetër në Evropë dhe është i endur nga një partner industrial i INES. Kjo uli gjurmën e karbonit me 75 gram CO2 për vat, krahasuar me një modul referimi me të njëjtën fuqi. Pesha ishte gjithashtu e optimizuar dhe është më pak se 5 kilogramë për metër katror.
"Ky modul ka për qëllim PV -në e çatisë dhe integrimin e ndërtesave," tha Derrier. "Avantazhi është se është natyrisht me ngjyrë të zezë, pa pasur nevojë për një fletë prapa. Për sa i përket riciklimit, falë termoplastikës, e cila mund të rimarrë, ndarja e shtresave është gjithashtu teknikisht më e thjeshtë. "
Moduli mund të bëhet pa përshtatur proceset aktuale. Derrier tha se ideja është transferimi i teknologjisë tek prodhuesit, pa investime shtesë.
"E vetmja e domosdoshme është të keni ngrirësit për të ruajtur materialin dhe të mos filloni procesin e ndërlidhjes së rrëshirës, por shumica e prodhuesve sot përdorin Prepreg dhe tashmë janë të pajisur për këtë," tha ajo.
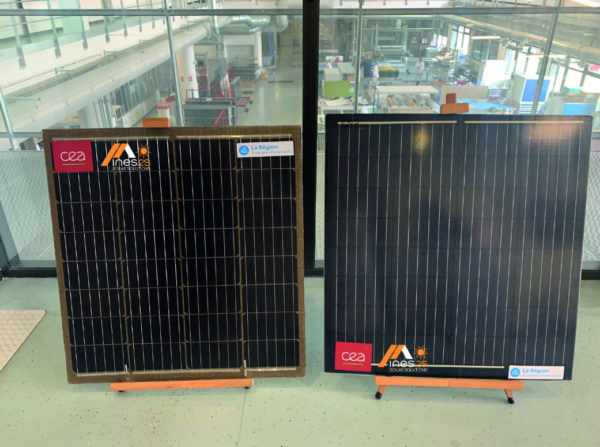
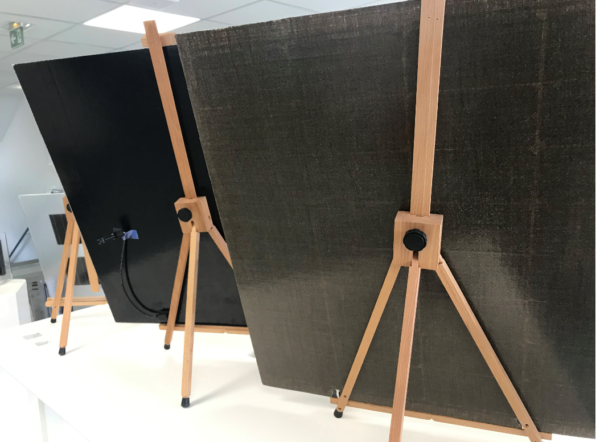
"Ne kemi punuar në jetën e dytë të qelqit dhe zhvilluam një modul të përbërë nga xhami i ripërdorur 2.8 mm që vjen nga një modul i vjetër," tha Derrier. "Ne kemi përdorur gjithashtu një encapsulant termoplastik i cili nuk kërkon ndërlidhje të kryqëzuar, e cila për këtë arsye do të jetë e lehtë për tu ricikluar, dhe një përbërës termoplastik me fibër liri për rezistencë."
Fytyra e pasme pa bazalt e modulit ka një ngjyrë natyrale prej liri, e cila mund të jetë estetikisht interesante për arkitektët për sa i përket integrimit të fasadës, për shembull. Për më tepër, mjeti i llogaritjes së INES tregoi një ulje prej 10% të gjurmës së karbonit.
"Tani është e domosdoshme të vihet në dyshim zinxhirët e furnizimit fotovoltaik," tha Jouini. "Me ndihmën e rajonit Rhône-Alpes brenda kornizës së Planit Ndërkombëtar të Zhvillimit, prandaj shkuam të kërkojmë lojtarë jashtë sektorit diellor për të gjetur termoplastikë të rinj dhe fibra të reja. Ne gjithashtu menduam për procesin aktual të petëzimit, i cili është shumë intensiv i energjisë. "
Midis presionit, shtypjes dhe fazës së ftohjes, petëzimi zakonisht zgjat midis 30 dhe 35 minuta, me një temperaturë operative prej rreth 150 C deri në 160 C.
"Por për modulet që përfshijnë gjithnjë e më shumë materiale të dizajnuara eko, është e nevojshme të transformoni termoplastikën në rreth 200 C deri 250 C, duke e ditur që teknologjia HTJ është e ndjeshme ndaj nxehtësisë dhe nuk duhet të kalojë 200 C," tha Derrier.
Instituti i Kërkimit është duke u bashkuar me specialistin e termocomepresionit të induksionit të bazuar në Francë Roctool, për të zvogëluar kohën e ciklit dhe të bëjë forma sipas nevojave të klientëve. Së bashku, ata kanë zhvilluar një modul me një fytyrë të pasme të bërë nga kompoziti termoplastik i tipit polipropilen, për të cilin janë integruar fibrat e ricikluara të karbonit. Ana e përparme është bërë nga termoplastika dhe tekstil me fije qelqi.
"Procesi i termocompression i induksionit të Roctool bën të mundur ngrohjen e dy pllakave të përparme dhe të pasme shpejt, pa pasur nevojë të arrijë 200 C në thelbin e qelizave HTJ," tha Derrier.
Kompania pretendon se investimi është më i ulët dhe procesi mund të arrijë një kohë cikli vetëm disa minuta, ndërsa përdor më pak energji. Teknologjia ka për qëllim prodhuesit e përbërë, për t'u dhënë atyre mundësinë e prodhimit të pjesëve të formave dhe madhësive të ndryshme, ndërsa integrojnë materiale më të lehta dhe më të qëndrueshme.
Koha e Postimit: Qershor-24-2022